an
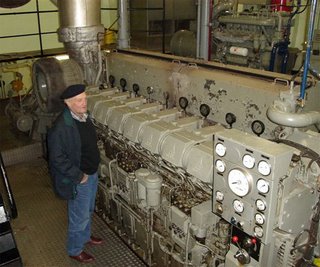
I started investigating the replacement options for our main engine even before I took delivery of the vessel.
The current 2.000 HP Deutz 628, 9 cylinder is a 'little oversized'. When trawling, a fishing vessel needs those 2.000 HP. When cruising as yacht, I can 10 knots using a 1/3 of that.
You can basically go to ways: keep the same mid-speed engine (750-900 rpm) or go to a high-speed engine (1800 rpm and up).
There's a lot of choice in the latter market but one big problem: you need a new reduction gear and your engine mounting

frame doesn't fit anymore.
In our case this issue become even more of a problem because the reduction gear recommended for the MTU engine we had in mind (8V MTU 4000) would require lowering the engine mount. That was going to be very expen$ive ! Add the new prop shaft, prop shaft seal and bearings, cooling water systems..... Ohh, and did I mention they have a delivery time of at least 18 months?
And a new reduction gear would also be around $ 40+ K.
So, we looked into a putting in a remanufactured 6 cylinder version of the current engine. But running the numbers on this, considering our typical use as an expedition yacht and the number of miles we'd actually be under way, we realized it would take us between 10 and 20 years before this investment would pay itself back, even if it would require running the current engine at a higher RPM (more

HP) to keep the engine from getting really dirty.
Spending a few $$ on fuel filters like those of CJC should keep this problem under control.
The blades of the 3.6 meter (11.6 ft) 4 blade
van Voorden prop will be adjusted to provide higher speed with the same amount of required power (or equivalent fuel savings) . This is a relatively cheap adjustment that will mean at least 10% higher speed. We expect to cruise at 10.5 to 11.5 knots.